sheet metal spring design MYD Metal has specialized in the customization of various sheet metal precision stamping parts and CNC machining for more than 15 years. . Our professional team and high-quality and efficient production capacity enable us to make . Yamaha controls are available for digital or mechanical rigs and tiller-handle controlled outboards, with some controls handling up to four outboards.
0 · spring steel strip 1mm
1 · spring steel sheet material grade
2 · spring steel material data sheet
3 · spring steel characteristics
4 · spring sheet metal and roofing
5 · spring back in sheet metal
6 · sheet metal spring back calculation
7 · high carbon spring steel properties
Many learner drivers do not understand the rules of yellow box junctions so i have compiled this video to help everyone not just learner drivers understand w.Yellow box junctions are indicated by criss-cross yellow lines painted on the road. They are usually found at the junction of two or more roads and occasionally at roundabouts or.
When stiffness and spring characteristics are required, the design engineer should consider the following: For parts with small radius forms, high carbon spring steel or another heat treatable .Blank holder helps prevent wrinkling and reduces springback. Blank holder not necessary if blank diameter / blank thickness is less than 25-40. Smaller values for deeper forming. . Designing an effective spring requires a thorough understanding of its operating environment, the application requirements, and the spring material’s physical characteristics. For designers and manufacturers to achieve optimal . Spring back of sheet metal parts after forming causes deviation from the designed target shape and produces downstream quality problems as well as assembly difficulties. It’s economic impact in terms of delayed production, tooling revision costs and rejection of unqualified parts is estimated to million/year in the U.S. automotive industry .
MYD Metal has specialized in the customization of various sheet metal precision stamping parts and CNC machining for more than 15 years. . Our professional team and high-quality and efficient production capacity enable us to make .The hardness of spring steel is commonly assessed using the Rockwell hardness scale, which gauges the depth of penetration of a diamond or tungsten carbide indent into the material. Spring steel typically exhibits a Rockwell hardness .
Master metal stamping and die design with this ultimate guide. Get expert tips and insights to improve your manufacturing processes. Start learning now. . Metal sheet specifications: steel strip, steel plate, slit steel strip, etc. Size range of steel plates and strips (GB/T708-2006)
Sheet metal deformation is purely an implementation of Stress-Strain curve characteristics. Spring back in Sheet Metals. . Living hinges must be designed, prototyped and created from scratch. Design is done using Computer Aided Software [CAD] whereas prototyping is done using one of the three major methodologies like CNC Machining (a . In sheet metal fabrication, the design of bends and flanges is instrumental in mitigating the spring-back effect and reducing the risk of metal tearing. Utilizing standard die sets, including 0.80 mm (0.030″) tools for internal corners, can be advantageous, or alternatively, consulting with your fabricator about the available tools is essential.Hi there! I am a professional mechanical & product designer..i have extensive knowledge 2d & 3d mechanical designs & product design in ( sheet metal, injection molding, plastic, wooden, aluminium, stainless steel, CNC Laser cutting etc. ) for printing, prototype, visualisation, 3d photrealistic rendering and manufacturing purpose..I have experience of 7 years in this field.I .Sheet metal spring. We develop and manufacture design-intensive sheet-metal components for the commercial and domestic products. The business area’s, product development is based on quality material and process know-how, that is renewed in an environment of competitive solutions of customer problems. An understanding of customers’ needs has .
This videos is related to spiral spring design in solid works by using helix /spiral command in solidworks sheet metal and also provides flat view by flatter.- 4 - Forming Near Holes – When a bend is made too close to a hole, the hole may become deformed. Figure "A" shows a hole that has become teardrop shaped because of this problem. To save the cost of punching or drilling in a secondary operation the following formulas can beImportance of the K-factor in sheet metal design. The K-factor is used to calculate flat patterns because it is related to how much material is stretched during bending. Therefore it is important to have the value correct in CAD software. The value of the K-factor should range between 0 – 0,5. To be more exact the K-factor can be calculated .Sheet Metal Forming 2.810 D. Cooper !“Sheet Metal Forming” Ch. 16 Kalpakjian !“Design for Sheetmetal Working”, Ch. 9 Boothroyd, Dewhurst and Knight . Examples-sheet metal formed . Female die Male die (punch/post) Metal sheet . Low spring back Al. 5052 H32 (10.6E6psi)
In the original design, the sheet metal required two separate bending processes. However, in the improved design, the sheet metal only needs one bending process to form the two sides at the same time. It is important to keep in mind that the more complex the bending process for the sheet metal, the higher the amount of material waste that may .
Figure 3 Coining, bottom bending, and air forming affect stressstrain properties differently. The curved line in the air forming zone shows how springback changes at different bend angles. In bottoming and coining, bending methods that usually produce 90-degree bend angles, the line curves to the right of the vertical axis, showing how the metal springs forward .Metal 3D Printing Design Guide. Direct Metal Laser Sintering (DMLS) 3D printing for parts with reduced cost and little waste. . metal springs have existed since the Bronze Age. Even before metals, wood was used as a flexible structural . As the bender moves down, the rocker makes contact with the sheet metal. One contact point acts as a holding pad, while the opposite contact point rotates, creating the bending action. After the bend is completed and on .Spring-back-effects-in-sheet-metals Technical Blogs, Skill-Lync offers industry relevant advanced engineering courses for engineering students by partnering with industry experts.
When the sheet metal is bent, the inner layer is subjected to compressive stress and the outer layer is subjected to tensile stress. Although these two stresses exceed the yield stress during elastic-plastic bending, in fact, there will always be an elastic deformation zone where the stress is lower than the yield stress when transitioning from tensile stress to . A kind of U type 90°or V type 90°bending springback testing die was set up to discuss the bending springback . The springback of material can be masteried through setting up of bending springback adjusting test die without prior calculation . In order to adjust the bending angle , the T type slide seat and bending press plate were used and the adjusting of bending . 5. Introduction (CONTD.) • The Progressive die or transfer die is dependent on size, complexity and volume of production. Progressive die stamping is used to produce a large number of parts and keep the costs as low as possible. The highest demands in precision and durability must be met Some of the metal-shaping techniques commonly used in progressive .The following are to links of sheet metal design resources, tools, articles and other useful data. Membership Services. Sheet Metal, Manufacturing, Design Equations and Calculations . Spring Design Apps Structural Shapes Threads & Torque Calcs Thermodynamics Physics Vibration Engineering Videos Design Manufacture
Material Spring-back: Different materials exhibit varying degrees of spring-back after bending. A properly calibrated K-factor accounts for this elastic recovery, allowing for more accurate prediction of the final bend angle and overall part dimensions. . How do I choose the appropriate K-factor for my sheet metal design? A: Selecting the .Sheet Metal Stampings; Stainless Steel Stampings; Wire Springs Menu . Atlantic Precision Spring is a USA manufacturer of flat springs and metal clips. We manufacture materials with thicknesses ranging from 0.003″ (0.076 mm) to 0.125″ (3.175 mm) and up to 12.00″ (304.8 mm) wide, depending on the intricacy. . Engineering assistance is .
7.1.1 Spring Design Procedures 1. Determine what spring rate and deflection or spring travel is required for your particular application. Also, determine the energy requirements. 2. Determine the space limitations in which the spring is required to work and try to design the spring accordingly, using a parallel arrangement if required, or allow .
In the final stage, all the contact forces are removed and the blank springs back to its final position, Fig. 4(d). Note the large deviation of the produced part shape from the die shape due to excessive springback. . Karafillis and M. C. Boyce, Tooling design in sheet metal forming using springback calculations, Int. J. Mech. Sci. 34, 113 .
2 talking about this
This guide explores sheet metal bending processes, materials suitable for bending, factors to consider and design tips for bending sheet metal parts. Search Now. Popular search terms. Contract Manufacturing; Plastic Injection; Contract Manufacturing; Stamping; Laser Cutting; Sheet Metal Fabrication; . Spring Steel .
cnc machining shop bowling green
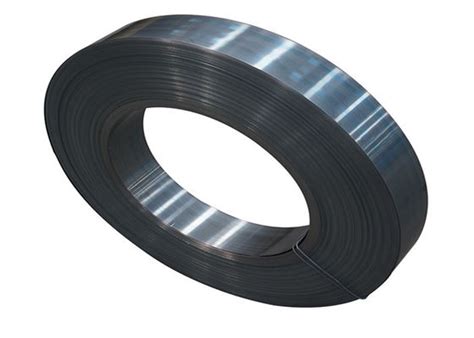
spring steel strip 1mm
spring steel sheet material grade

in Metal Fabricators, Fences & Gates, Garage Door Services. Reach out to .
sheet metal spring design|spring steel characteristics